Met behulp van de nieuwe Multifoiler thermovormmachine van de firma Robert Bürkle GmbH & Co. zijn drie-dimensionale schaaldelen van kunststof-folie te vervaardigen. Deze kunnen vervolgens in een standaard spuitgietoperatie achterspoten worden. Dit betekent niet alleen een aanzienlijke kostenbesparing maar ook een verbetering van de oppervlaktekwaliteit.
J.Düring en U.Kosok.
Voor allerlei toepassingen worden spuitgietprodukten gelakt, bedrukt (tampon- en zeefdruk), gecacheerd of gemetalliseerd. Een meer recente methode is het zogenaamde aquadec procédé [1]. Hierbij wordt een bedrukte speciale folie aan een waterbak toegevoerd. Door nu een produkt onder te dompelen vouwt de folie, met daarop de bedrukking, zich om het produktoppervlak.
In-mould-technieken
Bij alle zojuist genoemde methoden wordt uitgegaan van een gereed spuitgietprodukt waar achteraf een decoratie op aangebracht wordt. De alternatieve methoden, waarbij het aanbrengen van de decoratie niet achteraf maar in de matrijs plaats vindt, worden de zg. in-mould technieken genoemd.
Tot de in-mould technieken behoren niet alleen het achterspuiten van een folie of een andere vorm van decoratie zoals textiel maar ook het zg. in-mould-coating (IMC) procédé [3]. Een algemeen bekend in-mould proces is het zg. in-mould-decoration (IMD) waarbij een cacheer-folie vanaf een rol tussen de matrijshelften geleid wordt [2]. De folie bestaat uit een dragerfolie van veelal polyester waarop een reverse bedrukking en een hechtingslaag zijn aangebracht. Deze hechtingslaag wordt aangespoten en na het spuitgieten is de bedrukking op het produkt terug te vinden.
Het achterspuiten van relatief dikke decoratie materialen zoals een stof (textiel) of een geschuimd materiaal wordt voornamelijk toegepast in de automobielindustrie [4,5]. Hierbij wordt een op maat gemaakt stuk decoratiemateriaal in de matrijs bevestigd en achterspoten. Omdat er relatief dikke materialen achterspoten worden die indrukbaar zijn is een lage druk in de matrijs gewenst. De lagere druk wordt ondermeer gerealiseerd door gebruik te maken van het zg. lage-druk spuitgieten waarbij er geen of een zeer lage nadruk wordt toegepast. Dit veelal in combinatie met aangepaste spuitgietprocescondities.
Een andere wijze om een lagere druk in de matrijs te bewerkstelligen is het zg. spuitpersen of “Spritzprägen”, waarbij de matrijsholte maar gedeeltelijk gevuld wordt. De matrijs is dan als een zg. “Tauchkanten”-matrijs uitgevoerd en bij het vullen niet helemaal gesloten (staat enkele mm’s open). Na het gedeeltelijk vullen wordt de volledige sluitkracht aangebracht en wordt de matrijs volledig gesloten.
Combinatie
Kostentechnische redenen zijn een belangrijke drijfveer bij het zoeken naar alternatieve methoden om spuitgietprodukten te decoreren. Hierbij wordt veelal getracht de processtappen van het produceren en het decoreren te combineren wat dus tot de in-mould technieken heeft geleid. Onder de hoge druk van de voortbrengingskosten en de strenge kwaliteitseisen zijn de eerder genoemde in-mould processen niet zonder meer toepasbaar. Dit omdat bijvoorbeeld de beschikbare matrijzen en machines niet geschikt zijn of omdat de kosten van de decoratie materialen te hoog uitvallen.
Door de firma Robert Bürkle wordt nu voorgesteld om eerst een folieschaaldeel te vervaardigen en deze dan vervolgens in de voorhanden matrijs-machine configuratie te achterspuiten [7]. Door het combineren van de twee bewezen technieken thermovormen en spuitgieten wordt een aantrekkelijk alternatief verkregen. Als de gebruikte folie verder compatibel is met het substraat, wat er achter gespoten wordt, is het verwerken van uitval en het herverwerken van ingenomen oude produkten geen probleem. Bovendien wordt er een uitstekende hechting verkregen tussen folie en substraat.
Afhankelijk van het produkt kan het achterspuiten met een goedkoper recycle materiaal geschieden in plaats van een duurder veelal gepigmenteerd compound op basis van eerste klas materiaal. Het kostenvoordeel voor spuitgietprodukten met een relatief groot oppervlak en/of een grote massa, bijvoorbeeld dikwandige of geschuimde produkten, is met deze methode aanzienlijk. Maar ook het afdekken van het produktoppervlak waardoor allerlei spuitgiet defecten niet meer zichtbaar worden, zoals bijvoorbeeld bij veel gasinjectie produkten, kan een kosten voordeel opleveren.
Bij het gebruik van specifieke foliekwaliteiten kunnen de oppervlakte eigenschappen sterk verbeterd worden. Bijvoorbeeld als de folie een laklaag heeft die het spuitgietprodukt een verhoogde krasbestendigheid geeft. Ingeval van de laminaatfolies kunnen, afhankelijk van de topfolie, bijzondere eigenschappen verkregen worden. De laminaatfolies zijn opgebouwd uit meerdere folielagen waarbij, als gevolg van de ontwikkelingen in het gebied van de laminaatlijmen, zelfs incompatibele foliematerialen gecombineerd kunnen worden zoals bijvoorbeeld PMMA met PP.
Multifoiler thermovormmachine
Bürkle heeft eerst machines ontwikkeld voor het thermovormen van uiteenlopende PVC-folies van verschillende kwaliteiten en dikten. Door voortdurende aanpassingen en verbeteringen kan nu met de nieuw ontwikkelde BTF in principe elk thermoplastisch materiaal vervormt worden. Wezenlijk hierbij is de functie van een speciale verwarmingsplaat. De folie wordt door middel van contactwarmte snel op een, van de foliekwaliteit afhankelijke, temperatuur gebracht. Deze temperatuur ligt tussen bepaalde nauwe grenzen (operating window).
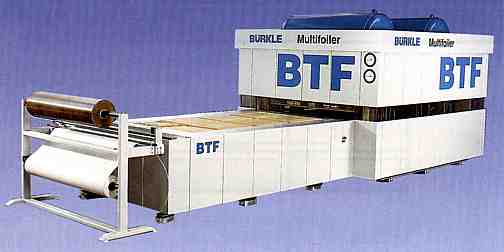
Het langs deze weg vervaardigen van folieschaaldelen is niet alleen zeer geschikt voor thermoplastische folies op basis van amorfe polymeren zoals van ABS, maar ook voor thermoplastische folies op basis van (semi-)kristallijne polymeren met een veel kleiner operating-window. Denk hierbij aan poly-olefine folies zoals van PP. Zelfs gelakte of laminaatfolies (ter bescherming van de opgebrachte decoratie of verhoging van de krasbestendigheid) met uiteenlopende dikten kunnen met deze machines probleemloos worde verwerkt.
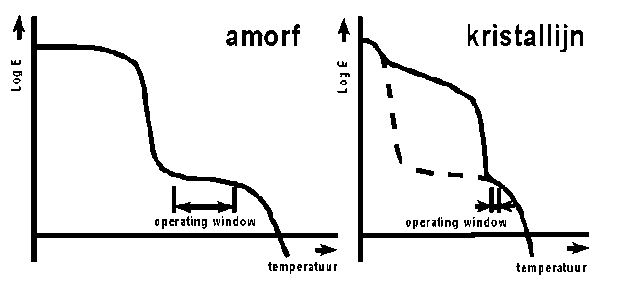
De BTF is ontwikkeld als een standaard machine welke in serieproduktie gefabriceerd wordt en een zeer bescheiden investering vraagt. Deze machine is een package-unit, er behoeft alleen maar elektra, perslucht en eventueel koelwater aangesloten te worden. De machine is enkele dagen na de montage al inzetbaar voor produktie en met het meegeleverde bedieningsconsole eenvoudig te bedienen.
De machine is in een aantal standaard afmetingen verkrijgbaar maar op aanvraag in afwijkende maten leverbaar. Hierdoor kan er voor elke gegeven situatie een optimale benutting van het persoppervlak gerealiseerd worden. In het persveld kan in één arbeidsgang één grote of meerdere kleinere folieschaaldelen vervaardigt worden. De folie kan direct vanaf een rol aan de machine toegevoerd worden. Het is echter ook mogelijk om vellen folie direct op de perstafel te positioneren. Indien gewenst kan de folietoevoer worden geautomatiseerd.
Om goede folieschaaldelen te vervaardigen zijn vormen nodig die dusdanig gedimensioneerd zijn dat onder andere rekening gehouden wordt met de krimp van de folie, het spuitgietprodukt alsmede de mechanische belasting bij het achterspuiten. Voor inleidende proeven of kleine produktieseries kunnen houtvormen van MDF gebruikt worden waarbij de kosten van deze vormen verwaarloosbaar zijn. Deze vormen zijn voor proefnemingen en een eerste indicatie van de eindkwaliteit van het produkt toereikend en kunnen makkelijk aangepast worden.
Voor een seriematige produktie van folieschaaldelen zijn echter vormen van metaal vereist, eventueel met koelkanalen uitgerust om een temperering van de vorm mogelijk te maken. De investering in zo’n vorm blijft bescheiden en is een percentage van de investering van de spuitgietmatrijs.
Wanneer de matrijs met betrekking tot ontluchting en voorziene vormgeving van het folieschaaldeel aan de vooropgestelde uitgangspunten voldoet kan met behulp van de bestaande matrijs-machine-configuratie worden geproduceerd.
De matrijs hoeft niet als een “Tauchkanten” matrijs uitgevoerd te zijn en er hoeft niet van speciale spuitgietmethoden zoals het lage-druk spuitgieten of het spuitpersen gebruik te worden gemaakt [4,5,6].
De folieschaaldelen kunnen elektro-statisch of met behulp van vacuumkleppen, als deze op de juiste plek aanwezig zijn, in de matrijs vastgehouden worden. De dimensies van de folieschaaldelen zijn voor het elektro-statisch plaatsen in principe geen probleem.
Tijdens het achterspuiten wordt de hechting tussen de folie en het substraat gerealiseerd en deze is ingeval van bijvoorbeeld PP-folie met PP uitstekend. Bij contact met het substraat smelt een laagje van de folie op en vermengt zich met het substraat.
Conclusie
Met behulp van de BTF zijn gecompliceerde folie schaaldelen te vervaardigen. Afhankelijk van de geometrie van het produkt is een ondersnijding goed mogelijk. Het bedekken van het spuitgietprodukt door bijvoorbeeld een uni-folie opent de mogelijkheid om goedkoper recycle materiaal in te zetten. Het bedrukken van de folie middels flexo-, diep- en zeefdruk geeft het produkt een bijzondere uitstraling en een geheel eigen meerwaarde. Het kiezen van de juiste folie kan de oppervlakte kwaliteit sterk verbeteren, bijvoorbeeld ingeval van een gelakte folie. De laklaag beschermt niet alleen de decoratie maar geeft het produkt ook een verhoogde krasbestendigheid.
Een ander aspect is dat het schaaldeel het oppervlak van het spuitgietprodukt bedekt en dat daarom spuitgietdefecten zoals vlekken, glansverschillen etc. niet meer zichtbaar zijn. Dit resulteert in een lagere uitval. Uiteindelijk biedt het achterspuiten van folieschaaldelen nieuwe interessante mogelijkheden ten aanzien van produktinnovatie en kostenrationalisatie alsmede een verbetering van de oppervlakte kwaliteit voor veel spuitgietprodukten zoals speelgoed, luxe gebruiksvoorwerpen, automobieldelen etc.
Literatuur.
[1] The revolution in surface decoration, Aquadec brochure van firma Aquagraphics, Corby (UK).
[2] Graff,G: In-mold-coating readies for industry debut, Modern Plastics International, February (1995), p.52-53.
[3] Böcklein, M: Das Battenfeld-Kurz-IMD-Verfahren-Dekorierung durch Hinterspritzen von Folien. Firmenschrift der Leonhard Kurz GmbH & Co, Fürth.
[4] Anders, S; Littek, W; Schneider, W: Hinterspritzen von Dekormaterialien durch Niederdruck-Spritzgießen. Kunststoffe 80 (1990) 9, S. 997-1002
[5] Mischke, J; Bagusche, G: Hinterspritzen von Textilien, Teppichen und Folien. Kunststoffe 81 (1991) 3, S. 199-203
[6] Jaeger, A; Fischbach, G: Maschinentechnik und Prozeßführung zum Dekorhinterspritzen. Kunstoffe 81 (1991) 10, S. 869-875
[7] Düring, J; Kosok, U.: Fertigung und Hinterspritzen von Kunststoff-Folienhauben, Firmenschrifft der Robert Bürkle GmbH & Co., Niederlassung “Westfalen”, Rheda-Wiedenbrück.