Réduction des frais et amélioration de la qualité de surface.
J.Düring et U.Kosok.
Le moulage par injection des matériaux décoratifs est une alternative moins coûteuse que les procédés conventionnels tels que le laminage, le tampon ou la sérigraphie et le matriçage à chaud etc. des pièces produites par injection. Un nouveau aspect dans ce domaine est le thermoformage d’un bonnet de feuille qui est formé par injection dans un moule à injection.
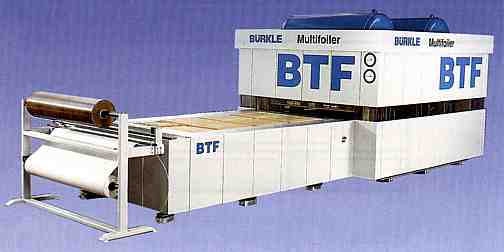
Un procédé de moulage par injection déjà bien connu est le procédé IMD (1). Dans ce cas une feuille à matricer à chaud mince provenant d’une bobine est posé entre les deux parties du moule de la machine d’injection. Pendant l’injection le décor est transféré sur la pièce moulée par injection et la feuille support est enroulée sur une autre bobine pour l’évacuation. Ce procédé sert donc à transférer des décor sur des pièces moulées par injection pour ainsi améliorer des articles en matière plastique coûteux. Surtout dans l’industrie automobile des matériaux décoratifs d’une épaisseur relativement élevée tels que des tissus ou de la mousse sont moulés par injection dans un moule à injection (2,3). A cause de l’augmentation des frais de production et les hautes exigences de qualité, il y a un grand nombre de produits pour lesquels les deux procédés de moulage par injection ne conviennent pas parceque soit les machines et moules disponibles ne sont pas utilisables soit les frais élevés des matériaux décoratifs s’opposent à ces procédés.
La Sté. Robert Bürkle à Rheda-Wiedenbrück présente une nouvelle solution économique, à savoir un programme en deux phases (5).
- Dans la première phase un bonnet à trois dimensions avec un repli jusqu’à 180 degrés est moulé dans la presse à thermoformage “multi-foiler”.
- Dans la duexième phase le bonnet est moulé par injection dans une machine d’injection (standard) jusqu’à ce que le produit désiré soit obtenu.
Lorsque la feuille est compatible avec le panneau support (par exemple moulage par injection d’une feuille PP avec du PP), il n’y a pas de problèmes de réutilisation des résidus dans la production et du recyclage des produits récupérés. L’utilisateur obtient une très bonne adhérence entre la feuille est la panneau support. Les machines pour le thermoformage des feuilles polyoléfines (feuilles PO) ont été dévelopées sur la base du “moulage des feuilles PVC”. En principe toutes les feuilles thermoplastiques peuvent être moulées. La machine pour le thermoformage à savoir la presse multifoiler permet également de produire des bonnets de formes compliquées avec des feuilles PO relativement minces. Ensuite ces bonnets peuvent être moulés par injection par le procédé de moulage par injection standard subséquent. Selon les produits moulés par injection, des matériaux récupérés bon marché peuvent être utilisés pour le moulage par injection sans être obligé d’utiliser des matériaux compoundés pigmentés très cher à base des matériaux de première classe. L’avantage de ce procédé est une économie de frais considérable dans la production des produits moulés par injection avec des surfaces relativement larges et/ou d’une grande masse (par exemple à paroi épais ou moussé). L’utilisation des feuilles d’une qualité appropriée permet également une amélioration considérable des propriétés de la surface. Pour citer un exemple, la feuille peut être munie d’une couche de vernis ce qui rend le produit plus résistant aux égratignures.
Concept de la chaîne.
Un facteur important de ce nouveau concept de la machine de thermoformage est la plaque chauffante spéciale. La feuille est chauffée précisemment et rapidement par la chaleur de contact qui convient à la qualité de feuille utilisée. Ce procédé de fabrication n’est pas seulement parfaitement approprié au thermoformage des feuilles PO telles que du PP mais aussi aux autres feuilles thermoplastiques telles que du ABS. Même des feuilles PP vernis (pour protéger le décor et/ou pour augmenter la résistance contre les égratignures) de différentes épaisseurs peuvent être utilisées. La chaîne est disponible en différents formats standard. Des dimensions spéciales permettent à tout moment une utilisation optimale de l’espace de pression qui permet également de fabriquer un grand bonnet de feuille ou plusieurs petits bonnets de feuilles dans une seule opération. La feuille peut être alimentée soit de la bobine soit découpée. La fabrication des bonnets de feuille exige des moules dont le dimensionnement tient compte de la contraction de la feuille et donc du produit moulé par injection ainsi que de la charge mécanique lors du moulage par injection. Pour des expérimentations initiales ou pour petites séries, des moules de bois en MDF peuvent utilisés. Les frais de ces moules sont peu importants. Ces moules de bois sont suffisants pour faire des essais d’évaluation de la qualité à obtenir du produit et permettent des adaptations nécessaires et des améliorations possibles. Pour une production en séries des bonnets de feuille il faut des moules en métal. Si absolument nécessaire, ces moules doivent être munis de canaux de refroidissement pour ainsi obtenir une optimalisation de la température. L’investissement pour ces moules est un minimum de ce qu’il faut pour des moules à injection. Quand le moule satisfait toutes les conditions concernant ventilation et moulage des bonnets de feuille, une production peut être démarrée avec la machine d’injection standard et les moules disponibles. Ni des moules qui s’enfoncent l’un dans l’autre ni un procédé injection spécial tel que le moulage par injection à basse pression ou le matriçage par injection (2,3,4) sont absolument nécessaires. Le bonnet de feuille est retenu dans le moule soit électrostatiquement soit par des soupapes à vide qui sont correctement positionnées. Les dimensions des bonnets de feuille ne posent pas de problèmes pour l’arrêtage électrostatique. L’adhérence entre la feuille et le panneau support est générée pendant l’injection et elle est excellent en cas de feuilles PP avec du PP par exemple. En contact avec la masse fondue une partie de la feuille fond et se mélange avec celle-ci.
Conclusion.
La machine de thermoformage permet la fabrication des bonnets de feuille compliqués. Selon la géométrie du produit un moulage avec un repli jusqu’à 180° degrés est possible. Le revêtement des produits moulés par injection avec une feuille unicolore par exemple permet l’utilisation des matériaux récupérés bon marché. L’utilisation d’une feuille décorative (appliquée soit par flexographie, rotogravure ou sérigraphie) donne au produit un aspect extérieur beaucoup plus précieux avec en comparison des produits non-décorés. Par ailleurs le choix de la feuille appropriée telle qu’une feuille vernie sert à améliorer les propriétés de la surface du produit moulé par injection. La couche de vernis ne protège pas seulement le décor mais en plus rend le produit plus résistant contre des égratignures. Un autre facteur très important est le recouvrement de la surface du produit par le bonnet de feuille et ainsi des défectuosités de l’injection telles que des taches etc. ne sont plus visibles. Ceci réduit les rebuts. L’injection des bonnets de feuille préfabriqués ouvre de nouvelle perspectives au point de vue économie des frais et amélioration de la qualité des surfaces pour bien des produits moulés par injection par exemple des jouets, des objets d’usage courant etc.
Literature
[1] Böcklein, M: Das Battenfeld-Kurz-IMD-Verfahren-Dekorierung durch Hinterspritzen von Folien, Firmenschrift der Leonhard Kurz GmbH & Co, Fürth.
[2] Anders, S; Littek, W; Schneider, W: Hinterspritzen von Dekormaterialien durch Niederdruck-Spritzgießen. Kunststoffe 80 (1990) 9, S. 997-1002.
[3] Mischke, J; Bagusche, G: Hinterspritzen von Textilien, Teppichen und Folien. Kunststoffe 81 (1991) 3, S. 199-203
[4] Jaeger, A; Fischbach, G: Maschinentechnik und Prozeßführung zum Dekorhinter-spritzen. Kunststoffe 81 (1991) 10, S. 869-875.
[5] Düring, J; Kosok, U.: Fertigung und Hinterspritzen von Kunststoff-Folienhauben, Firmenschrifft der Robert Bürkle GmbH & Co., Niederlassung “Westfalen”, Rheda-Wiedenbrück.