Cost reduction and an improved surface quality.
J.Düring and U.Kosok.
Back moulding of decorative materials is a less expensive alternative to conventional processes such as laminating, lacquering, tampon or serigraphy (screen printing), hot stamping etc. of injection moulded parts. A new development in this field is the thermo-forming of a foil into a shape which is back-moulded in the injection mould
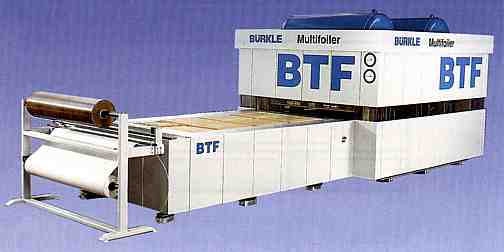
An already known back-moulding process is the IMD-process [1]. With this process a thin foil suitable for hot stamping is uncoiled from a roll and placed between the two halves of the mould of the injection moulding machine. During injection moulding decoration is transferred onto the injection moulded part and the supporting foil is coiled onto another roll for disposal. This process is used for transferring decorations onto injection moulded parts to upgrade costly plastic articles. Another process used extensively in the automobile industry is one where comparatively thick decorative material such as textiles or foams are back moulded in the injection mould [2,3].Due to increasing production costs and the high standards of quality, the above two mentioned moulding processes are not necessarily suitable for many injection moulded articles. Either the available machines and moulds cannot be used or the high cost of the decorative materials make the process un-economical.
As a new economic solution Robert Bürkle in Rheda-Wiedenbrück presents a new two step process [5].
- In the first step the thermo-forming machine “Multifoiler” generates a three dimensional shape with a bend of p to 180 degrees
- In the second step the shape is back-moulded on a (standard) injection moulding machine till the desired part is obtained.
If the foil is compatible with the substrate (for example back-moulding of a PP-foil with a PP) no problems arise regarding the re-use of left over materials from production and the recycling of old products. Additionally an excellent bond is obtained between the foil and the substrate. The Machines for thermo-forming polyolefine foils (PO-foils) were developed based on machines for “forming PVC-foils” In principle all thermoplastic foils can be formed. The Multifoiler thermo-forming machine permits also the production op complicated shapes with comparatively thin PO-foils. these shapes can then be back-moulded in the subsequent standard injection moulding process. Depending on the injection moulded part, cheap recycled material can be used for injection moulding without being forced to use more expensive pigmented compounds based on first class material. This new process allows a considerable cost saving producing parts with a comparatively large surface and/or a lot of material mass (for example thick walled or foamed). When using foils of suitable quality, the properties of the surface can be considerably enhanced. For example, the foil can be provided with a coat of lacquer which makes the injection moulded part more resistant to scratches.
Machine concept
An essential factor of this new concept of the thermo-forming machine is a special heating plate. The foil is heated precisely and very quickly by contact heat which corresponds to the quality of the foil. This production process is not only well suited for thermo-forming PO-foils such as PP, but also fur other thermoplastic foils such as ABS. Also lacquered PP-foils (to protect the decoration and/or to give a higher resistance against scratches) of different thicknesses can be used. The machine is available in a range of standard sizes. Special sizes allow an optimal utilization of the forming area for all situations. In this pressing area one large or several small foil shapes can be produced in one operation. The foil can be either fed from a roll or ready cut to size. Moulds are required to produce the foil shapes. the dimensions of these moulds must take account of the shrinkage of the foil and the moulded article as well as the mechanical load during injection moulding. For prototypes or small production runs, wooden moulds made of MDF can be used. The costs of these moulds are insignificant. Such wooden moulds are sufficient for tests and evaluations of the final quality of the product and allow any necessary modifications to be made, they also give scope for enhancement. Moulds made of metal are required for mass production of foil shapes. To allow an optimal temperature equalization, these moulds are equipped with cooling channels if absolutely necessary. The Investment capital for these moulds is only a fraction of that required for the injection moulds If the injection mould meets the requirements regarding ventilation and moulding of the foil shape, production can be started with the available moulds and the standard moulding machines. These injection moulds must not necessarily dip in one each other, nor is a special injection moulding process required such as low pressure injection moulding or injection stamping [2,3,4]. The foil shape is either electrostatically held down in the mould or by means of suitably located vacuum valves. The dimensions of the foil shape present no problem for electrostatic fixing. The bonds between foil and substrate is achieved during injection moulding and is excellent in the case of PP-foils with PP for example. Once in contact with the molten material part of the foil melts and combines with the molten PP.
Conclusion
The thermo-forming machine allows the production of complicated plastic foil shapes. Depending upon the geometry of the product, a mould with a bend of up to 180 degrees is possible The coating of injection moulded parts with for example a single coloured foil (uni-foil) opens up new opportunities for the use of cheap recycled material. A decorative foil (applied either by flexographic printing, rotogravure or serigraphy)embellishes the product and gives it a luxurious feel in comparison to non-decorated articles. The surface properties of the injection moulded part can be enhanced by choosing the most suitable foil such as lacquered foil. The coat of lacquer not only protects the decoration but also makes the product more resistant to scratches. A further very important benefit is that the foil shape covers the surface of the product and thus any defects which occur during the injection moulding process such as stains etc. are hidden, this results in a reduced reject level. Injection moulding of prefabricated foil shapes enables costs to be reduced and gives improved surface quality for many injection moulded parts such as toys and various other articles which are used daily.
Literature
[1] Böcklein, M: Das Battenfeld-Kurz-IMD-Verfahren-Dekorierung durch Hinterspritzen von Folien, Firmenschrift der Leonhard Kurz GmbH & Co, Fürth.
[2] Anders, S; Littek, W; Schneider, W: Hinterspritzen von Dekormaterialien durch Niederdruck-Spritzgießen. Kunststoffe 80 (1990) 9, S. 997-1002.
[3] Mischke, J; Bagusche, G: Hinterspritzen von Textilien, Teppichen und Folien. Kunststoffe 81 (1991) 3, S. 199-203
[4] Jaeger, A; Fischbach, G: Maschinentechnik und Prozeßführung zum Dekorhinter-spritzen. Kunststoffe 81 (1991) 10, S. 869-875.
[5] Düring, J; Kosok, U.: Fertigung und Hinterspritzen von Kunststoff-Folienhauben, Firmenschrifft der Robert Bürkle GmbH & Co., Niederlassung “Westfalen”, Rheda-Wiedenbrück.