A THERMOFORMING machine specifically configured to produce preforms for finishing injection mouldings has been produced by the German firm Robert Bürkle & Co. In-mould finishing has been adopted in some applications as an alternative to post-moulding operations such as laminating, lacquering, pad or screen printing or hot stamping to eliminate further processing of the part, to remove solvent fume emission, or to improve part aesthetics by producing a moulded-in finish. The two processes most frequently used are moulding against a foil fed from a continuous reel and clamped between the mould halves to give a printed/lacquered surface, and a similar process to apply a thick material such as a textile or foam. However, according to Rober Bürkle’s John Düring, these processes are not suitable for many injection mouldings because either the available machines and moulds cannot be used, or the high cost of the decorative materials makes the process uneconomical.
The company’s Multifoiler has been designed to produce a three dimensional surface shape which can be inserted into the mould to become an integral part of the moulding. By taking this route, a moulder can achieve a quality surface while, for instance, using recycled materials, or using a moulding process not noted for its surface finish, such as a structural foam. And the use of a foil preform which has been lacquered provides protection against abrasion of the decoration, and can improve the overall surface gloss and texture. These arguments apply for the established in-mould foiling processes, but Mr Düring says that the foils used for these processes are more expensive than those used in the Multifoiler, have much thinner lacquer layers, and do not allow undercuts. While in theory these preforms could be produced on conventional thermoforming machines, the nature of the thin, lacquered foils used calls for a machine with a modified mode of operation, hence the Multifoiler. The primary difference is the way the foil is heated. On conventional thermoformers the heating of the sheet takes place separate from the forining station to speed up throughput, and is applied with radiant emitters.The Multifoiler uses a closed chamber with a contact heating plate. This achieves two aims. Firstly, it prevents the overheating of the foil surface which could result from using radiant heaters, but instead generates a uniform temperature through the foil. Overheating the surface can damage the lacquer and decoration layer, and a non-uniform temperature produces areas of higher tension which can break the lacquer and/or the foil. Secondly, when the foil is heated it is preferable not to move it, as the inevitable changes in temperature can, again, produce areas of higher tension. Even if the lacquer and/or foil do not break, a non-uniform temperature can give non-uniform surface gloss. A further possible problem with overheating is that any surface texturing may be lost.
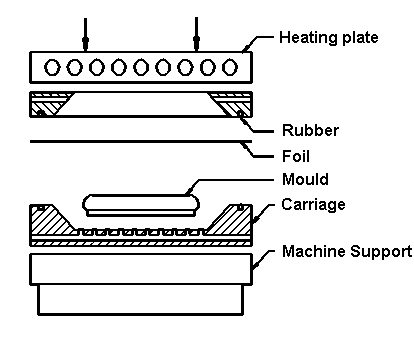
Mention of non-uniform temperature breaking the lacquer begs the question of what happens to the lacquer during the normal forming process. The answer is that the lacquer used on these foils has been specially developed for the purpose and is itself thermoformable. Its nature is guarded by the companies making the foils, of which Mr Düring says there are some half dozen in Europe. Introduction to an appropriate foil supplier is part of the total package being offered by Bürkle. The accuracy of the temperature control is also important to enable the process to be used with the broad spectrum of plastics materials. Amorphous polymers such as ABS have a reasonable forming ‘window’ but for crystalline and semi-crystalline materials -such as polypropylene – this ‘window’ is much smaller and accurate temperature control is more critical.
The forming process is to clamp the foil between the machine platens and evacuate the space between the foil and the heating plate, allowing the foil to be sucked into intimate contact with the heater. This plate is electrically heated, and has oil channels for further temperature control. After heating, air is returned above the foil and the space below it is evacuated as in conventional forming, wrapping the foil round the form. Substantial undercuts can be achieved with the aid of increased air pressure above the foil. The moulds used can be of wood/MDF for prototyping and short production runs, with metal tooling for full production. Mould costs are a fraction of those used for injection moulding. The point emphasised by the company is that this process can be introduced on existing injection mould tooling – with the caveat that appropriate venting must be in place – and using conventional machines. The assumption is that some form of pick and place device is already in use for product removal, and that this can be adapted to place the foil in the mould. All that has to be added is a means of retaining the foil. Vacuum valves could be inserted but they can leave surface impressions and are expensive to move. The preferred option is electrostatic pinning, which requires no modification. An electrostatic system is reckoned to cost around DM 10,000 and can be installed on the pick and place robot, which Mr Düring says is a significantly cheaper option than the foil handling devices needed above and below the mould when using the established in-mould foiling processes.
The Multifoiler is built in several forming sizes and can be set up to produce families of preforms in a single cycle. By combining thermoforming with injection moulding in this way the company sees a number of opportunities to enhance conventional injection moulding. Use of a single coloured foil gives a coloured surface – indeed a range of coloured surfaces – without needing to use coloured virgin material, and in fact using just a single supply of, possibly, lower cost recycled material. Adding the surface in this way circumvents rejects through surface blemishes produced by the moulding process. And the lacquered surface makes the decorative finish more abrasion resistant.
When the technology was announced in Germany last year it generated interest from a variety of market segments, including garden furniture, bathroom furniture and the automotive industry.