The need for flexibility in moulding technologies has led to a number of variations on the basic injection moulding machine which enable different moulding processes to be carried out without substantial investment in dedicated equipment.
Multi-material moulding is ever-more commonplace, with additional injection units being supplied for standard machines to enable them to be converted for multi-component or sandwich moulding, but still to be available for moulding in more conventional configurations.
One such conversion system has been in use in Japan since 1999, and is now being promoted in Europe by the Dutch company Mercatel Groep. This is the Master Mould Plates System in which an adapter on the fixed platen carries a second injection unit, and also manages the injection unit of the two melt streams. This second injection unit can be positioned vertically or horizontally are right angles to the machine axes.
The adapter is a slim unit which has only a small effect on the hydraulic shot off for the second melt stream – the core material in a sandwich moulding operation – which send both melt streams through the same channel, effectively making the flow channels in the adapter self-cleaning.
Machines using the MMP system are moulding bumpers containing recycled material for Honda and Nissan, and also components for Canon and Sony office machines. Other applications are in larger flat parts such as TV cabinets, and more complex products such as crates, pallets and more recently office furniture parts.
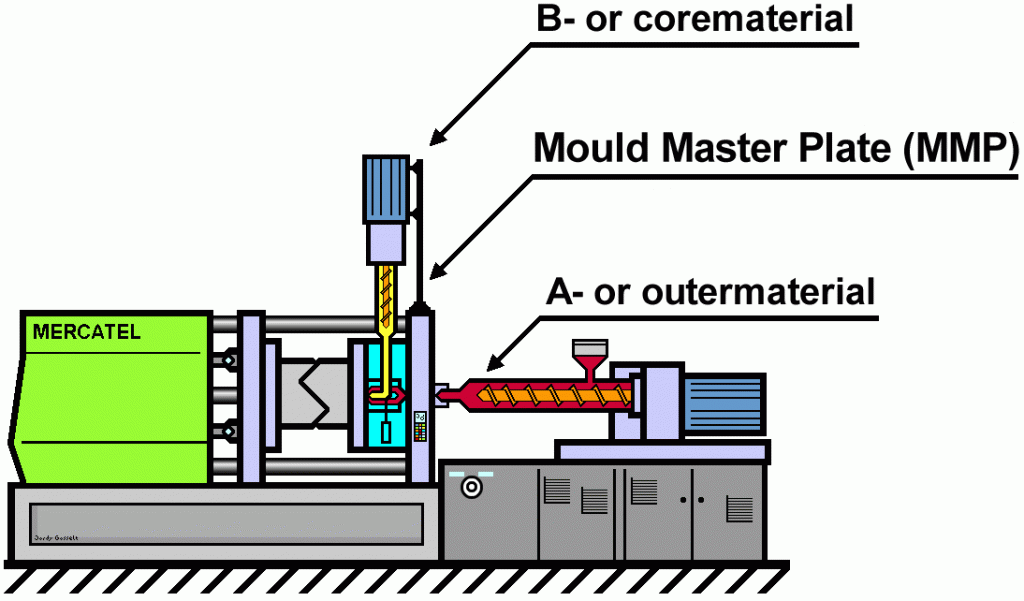
The MMP system is also seen as an answer to scrap reclaim. As companies are forced to recycle their end-of-life products there is a need to overcome the incompatibility of the reground scrap with new production. Canon faced this problem with recycled ABS/PC from office machine housings which would have required expensive compounding to make it reusable as a surface material, but by using the MMP system it was able to re-use the reclaimed chips directly as a core material up to 30 per cent at a thickness of 3 mm, with considerable savings.
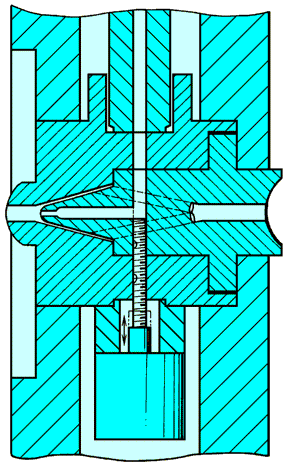
The MMP system can be brought into play for sandwich and/or 2 -component
moulding, but when the machine is to be used for conventional single material
moulding the adapter doesn’t need to be removed: it can remain on the fixed
platen until it is needed again, so there is no downtime from stopping the
machine for assembly and disassembly.
The MMP system was devised for use on large machines, but smaller systems have
been built – and custom-designed adapters are now also available.